Abstract
The integration of intelligent design software into high-end jewelry design has revolutionized traditional craftsmanship, enabling unprecedented precision and creativity. However, questions persist about whether these tools can genuinely comprehend and replicate the intricate artistry embedded in luxury jewelry. This article explores the capabilities, limitations, and future potential of AI-driven technologies in bridging the gap between digital innovation and artisanal mastery.
1. Introduction: The Evolution of Jewelry Craftsmanship
High-end jewelry has long been synonymous with meticulous handcrafted techniques, such as hand-engraving, stone setting, and metal forging. These processes require decades of expertise and an intimate understanding of materials like gold, platinum, and gemstones. In recent years, intelligent design software—powered by AI algorithms, 3D modeling, and machine learning—has emerged as a transformative force. While these tools enhance efficiency and expand creative possibilities, their ability to replicate or innovate within the realm of traditional craftsmanship remains debated.
2. Capabilities of Intelligent Design Software
2.1 Algorithmic Analysis of Design Elements
Modern AI systems excel at dissecting and reconstructing design elements. By analyzing vast datasets of historical and contemporary jewelry, algorithms can identify patterns in shapes, textures, and material combinations. For example, AI tools generate design variations by recombining elements like filigree patterns or Art Deco motifs, offering designers a starting point for further refinement .
2.2 Precision in Complex Geometry
3D printing technologies, integrated with AI-driven design software, allow for the creation of geometrically intricate structures that are nearly impossible to achieve manually. Techniques like selective laser sintering (SLS) enable the production of jewelry with hollow architectures, interlocking components, or microscale textures. Brands like Cartier and Boucheron have utilized such technologies to produce avant-garde pieces that retain traditional elegance .
2.3 Optimization of Production Workflows
AI enhances efficiency across the production chain. For instance:
- Smart Scheduling: Algorithms analyze order volumes and resource availability to optimize manufacturing timelines.
- Quality Control: Machine vision systems detect microscopic defects in gemstones or metal castings, ensuring adherence to luxury standards .
3. Limitations in Replicating Traditional Craftsmanship
3.1 The Nuances of Handcrafted Artistry
While AI excels at technical precision, it struggles to emulate the human touch inherent in haute joaillerie. Techniques like hand-engraving or pavé setting rely on subtle variations in pressure and angle, which are shaped by an artisan’s intuition and experience. Algorithms lack the sensory feedback and contextual awareness required to replicate these nuances fully.
3.2 Material Sensitivity and Adaptability
Luxury jewelry often employs rare or delicate materials (e.g., jade, opals) that demand adaptive handling. Intelligent software may miscalculate material behavior under stress or fail to account for natural variations in gemstone clarity and color. For example, an AI-generated design might propose a fragile prong setting for a brittle emerald, whereas a master jeweler would adjust the structure based on tactile feedback .
3.3 Cultural and Aesthetic Interpretation
High-end jewelry is deeply rooted in cultural narratives and symbolic meanings. AI’s data-driven approach risks oversimplifying these contexts. A algorithm might generate a technically flawless Indian Kundan-style necklace but miss the spiritual significance of its gemstone arrangements, which are traditionally guided by Vedic principles.
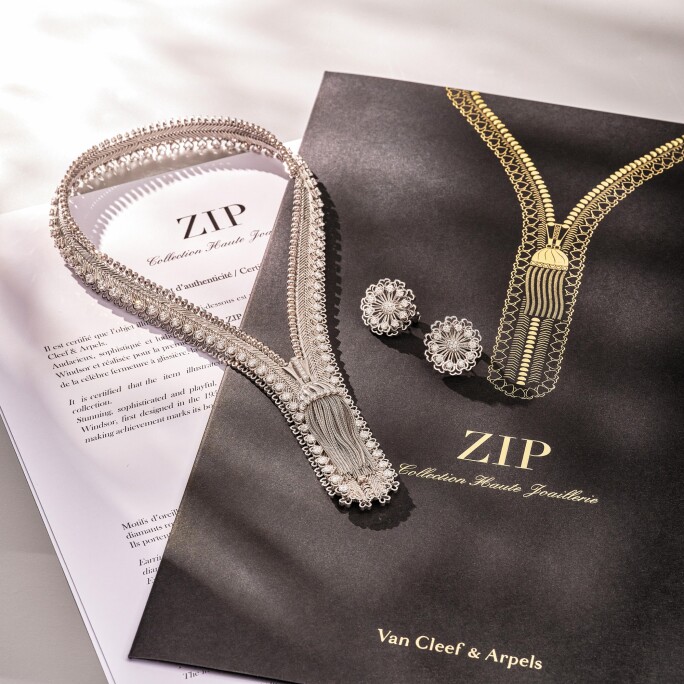
4. Case Studies: Bridging Technology and Tradition
4.1 Van Cleef & Arpels’ Hybrid Approach
The French maison combines AI-generated prototypes with hand-finishing. For its Alhambra collection, AI software produced hundreds of clover motif variations, which artisans then refined by hand to ensure the pieces’ organic flow and balance .
4.2 3D-Printed Titanium Masterpieces
Independent designers like Joshua Deuchel use AI-optimized 3D printing to create lightweight titanium necklaces with lattice structures. While the software handles structural integrity calculations, Deuchel manually adjusts surface finishes to evoke a hand-forged aesthetic .
4.3 Ethical Gemstone Sourcing via Blockchain-AI Integration
Companies like GemGenève employ AI to trace gemstone origins and ensure ethical sourcing. This technological layer complements traditional craftsmanship by adding transparency—a growing priority for luxury consumers .
5. Future Directions: Toward Symbiosis
5.1 Enhanced Material Databases
Future AI systems will incorporate richer datasets on material properties, such as the ductility of 18K gold or the refractive indices of sapphires. This will improve software’s ability to simulate real-world behaviors during the design phase.
5.2 Human-AI Collaborative Interfaces
Emerging platforms like Adobe’s Project Gemini aim to create intuitive interfaces where designers and AI co-create in real time. For example, a designer sketching a brooch might receive AI suggestions for gemstone placements that enhance light reflection, while retaining final artistic control .
5.3 Sustainability-Driven Innovations
AI can minimize material waste by optimizing 3D printing layouts or recycling metal powders. Brands like Chopard are already using AI to design zero-waste collections that align with circular economy principles .
6. Conclusion: The Artisan’s Tool, Not Replacement
Intelligent design software is redefining the boundaries of high-end jewelry but remains a tool rather than a substitute for human artistry. Its true potential lies in augmenting traditional techniques—enabling artisans to explore bolder designs, conserve resources, and meet evolving consumer demands. As technology advances, the synergy between AI and craftsmanship will likely yield new forms of luxury that honor heritage while embracing innovation.