The world of jewelry design is evolving rapidly as new technologies open up exciting possibilities for designers to enhance the intricacy, refinement, and functionality of their creations. Traditionally, jewelry was crafted by hand, relying heavily on artisanal skills passed down through generations. However, in the modern era, advancements in technology are reshaping the landscape of the jewelry industry, allowing designers to push boundaries and create pieces that are more precise, innovative, and functional than ever before.
From 3D printing to CAD (Computer-Aided Design) and augmented reality (AR), new technologies have provided jewelry designers with tools that can improve both the aesthetic and practical aspects of their designs. In this article, we will explore how designers are incorporating these cutting-edge technologies to enhance the craftsmanship, precision, and usability of their jewelry, ultimately leading to more refined, personalized, and functional pieces.
1. 3D Printing: A Game-Changer for Jewelry Design
A. Precision and Intricacy
One of the most transformative technologies in modern jewelry design is 3D printing. This technology has revolutionized the jewelry-making process, enabling designers to create complex and detailed designs with incredible precision. 3D printing allows designers to craft intricate shapes, patterns, and textures that would be extremely difficult, if not impossible, to achieve with traditional handcrafting techniques.
For instance, designers can create highly detailed filigree patterns, delicate lacework, or geometrically complex structures that have fine details and can be reproduced exactly as intended. The precision of 3D printing also allows for less material waste, which is not only more sustainable but also cost-effective.
With 3D printing, jewelry designers can experiment with abstract and avant-garde designs that were once limited by the constraints of traditional crafting methods. This technology has opened the door to a new era of artistic freedom where the only limitation is the designer’s creativity.
B. Customization and Personalization
One of the major benefits of 3D printing in jewelry design is the ability to customize pieces to meet individual client specifications. Customers can now participate more actively in the design process by selecting materials, shapes, and even providing input on textures. Designers can then use 3D printing to create bespoke, one-of-a-kind pieces that reflect the client’s personal style or significant life moments.
This level of customization has made 3D printing especially popular in the realm of engagement rings and wedding bands, where couples seek unique, meaningful designs. Moreover, this technology allows for the creation of personalized engravings or monograms, further enhancing the emotional value of the jewelry.
C. Rapid Prototyping and Experimentation
Another advantage of 3D printing is the ability to rapidly create prototypes of jewelry designs. Designers can produce digital models of their designs, print them, and evaluate them in the physical world before making final adjustments. This trial and error process is much faster and more cost-effective than traditional methods, where a designer might need to create physical prototypes using precious materials.
Through rapid prototyping, designers can fine-tune their designs and test different materials and finishes before committing to the final piece. This ensures that the final product is not only aesthetically pleasing but also practical and functional.
2. Computer-Aided Design (CAD): Precision and Innovation in Jewelry Creation
A. Detailed and Accurate Design
CAD (Computer-Aided Design) software has become an indispensable tool for modern jewelry designers. It enables them to create highly detailed and precise digital models of their jewelry pieces, ensuring that every aspect of the design is perfect before it is manufactured. With CAD, designers can adjust and manipulate every part of the piece, from the gemstone settings to the metal work, ensuring that the proportions, textures, and fit are flawless.
CAD also allows designers to experiment with new design concepts and create highly detailed 3D models that can be viewed from any angle. This digital approach eliminates the need for hand-sketching or the time-consuming and often error-prone process of creating physical prototypes. It also allows for easier revisions and updates to designs, saving both time and resources.
B. Simulation of Materials and Finishes
CAD software allows designers to simulate different materials and finishes on a digital model, enabling them to visualize how various metals, gemstones, and textures will interact with one another. Designers can test out combinations of precious metals (such as gold, platinum, and silver) with gemstones (such as diamonds, sapphires, and rubies) to see how they work together before committing to the physical production of the piece.
This capability ensures that designers can make informed decisions about the materials used, resulting in pieces that are visually stunning and structurally sound. Additionally, CAD allows for the creation of realistic renderings that can be shared with clients, helping them better visualize the final product and make any necessary adjustments before production.
C. Integration with 3D Printing and CNC Machines
CAD software is often integrated with other technologies such as 3D printing and CNC (Computer Numerical Control) machines, which enable designers to bring their digital models to life. These technologies allow for the accurate manufacturing of the designer’s digital models, turning them into physical pieces with remarkable precision.
By using CNC milling or casting, designers can take the intricate digital models created in CAD and produce them in a range of materials, from high-quality metals to precious stones. This integration streamlines the production process and ensures that the final piece matches the designer’s original vision.
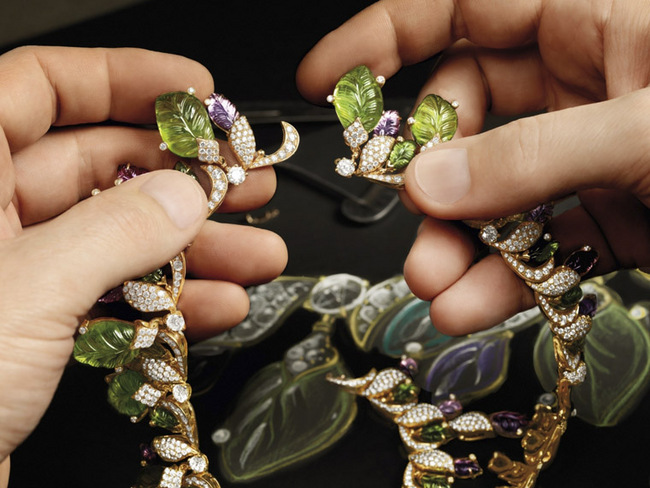
3. Augmented Reality (AR): Enhancing the Jewelry Buying Experience
A. Virtual Try-Ons
Augmented Reality (AR) is another innovative technology that is shaping the jewelry industry. AR allows consumers to virtually “try on” jewelry before making a purchase, without physically wearing the piece. By using smartphones or AR-enabled devices, customers can see how a ring, necklace, bracelet, or pair of earrings looks on them in real-time through a digital interface.
For jewelry designers, AR provides a powerful tool for engaging customers and allowing them to explore different designs and personalized options before committing to a purchase. It also helps reduce the risk of returns, as customers are able to get a more accurate sense of how a piece will look on them in terms of size, fit, and style.
B. Design Visualization
For designers, AR can also be used as a design tool to visualize how different pieces of jewelry will look on a person before the final piece is created. Using AR, designers can superimpose their digital jewelry models onto a person’s image, helping them understand how proportions, size, and design choices will affect the final result.
This can be especially helpful in the customization process, where designers can create personalized pieces for clients based on their unique body types, preferences, and personal style. By visualizing the designs in AR, clients can make more informed decisions and feel confident in their choices before the jewelry is crafted.
4. Laser Technology: Precision and Intricate Detailing
A. Laser Engraving and Cutting
Laser technology has become an essential tool in modern jewelry design, offering designers the ability to create highly detailed engravings and precise cuts. Laser engraving allows designers to add intricate patterns, logos, or personalized messages to jewelry pieces with remarkable precision. This technology ensures that the engraving is clean, fine, and consistent, allowing for more detailed work than traditional hand-engraving methods.
Laser cutting, on the other hand, allows designers to cut and shape metals with extreme accuracy, enabling them to create geometrically complex and delicate structures that would be difficult to achieve by hand. This technology also allows for reduced material waste, as the cuts are extremely precise, ensuring that precious materials are used efficiently.
B. Enhancing Functionality
Laser technology is also improving the functionality of jewelry. For example, designers can use lasers to create hidden compartments in jewelry pieces, allowing for the storage of small items like photos, messages, or even GPS chips for tracking purposes. This enhances both the aesthetic and practicality of the jewelry, making it not just a decorative piece but also a functional accessory.
5. The Future of Jewelry Design: Innovation Continues
The integration of new technologies into jewelry design is allowing designers to create pieces that are not only more intricate and beautiful but also more functional and personalized. With tools like 3D printing, CAD software, AR, and laser technology, jewelry designers are pushing the boundaries of what is possible, offering clients a new level of customization, creativity, and innovation.
As technology continues to evolve, the jewelry industry is poised for even greater transformations. New materials, techniques, and tools will further enhance the precision, quality, and versatility of jewelry designs. Designers who embrace these technological advances will be able to craft pieces that are not only works of art but also highly functional and tailored to individual needs.
In the end, technology is not replacing the artistry of jewelry design; rather, it is expanding the possibilities for designers to create even more refined, personalized, and innovative pieces that meet the demands of today’s consumers. The future of jewelry design is undoubtedly bright, with technology playing an integral role in shaping its evolution.